What is Surface Mount Technology?
SMT is Surface Mounted Technology. Surface Mounted Technology is the most popular Technology and process in the electronic assembly industry. SMT Surface Mounted Technology assembly refers to the abbreviation of a series of technological processes based on PCB. Printed Circuit Board (PCB) is a Circuit assembly technology in which unleaded or short lead surface assembly components (SMC/SMD) are installed on the surface of a Printed Circuit Board, and soldered together through reflow or dip soldering. All electronic products are through a circuit design, and the installation of capacitors, resistors, integrated circuits, connectors, and other electronic components on the PCB is usually completed by the SMT process.
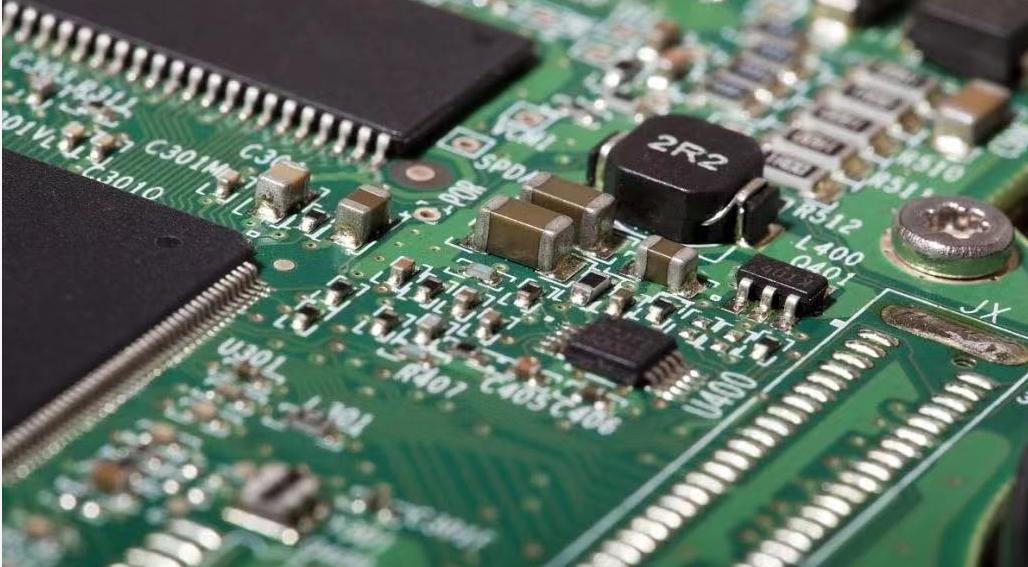
Surface Mount Technology Applications
Since the first smt surface mount technology circuit launched by Philips, SMT surface mount technology has been mainly used in military, aviation, aerospace and other cutting-edge products and investment products, and gradually applied to computer, communications, military, industrial automation, consumer electronics and other industries. SMT technology developed very rapidly, and in the 1980s, SMT technology has become the most popular new generation of electronic assembly technology.
Development of SMT Package Components
SMT package components are mainly surface mount components SMC, SMD, and SMB.
(1) SMC is developing toward miniaturization and large capacity. The latest SMC specification is 01005, in the volume miniaturization at the same time to the large capacity direction development.
(2) SMD is developing in the direction of small volume and multi-pins. SMD went from large volume, small pins to large volume, multi-pins directions development, now has begun from large volume, multi-pin direction to small volume, multi-pin direction, such as BGA to CSP direction development. The application of FC will be more and more.
(3) SMB is developing towards multi-layer, high density and high reliability. As electronic assembly moves toward higher density, many SMB board layer number has up to a dozen or even more, multi-layer flex SMB has also developed rapidly.
Advantages and Disadvantages of Surface Mount Technology (SMT)
With the development of social science technology, the continuous reconstruction and development of the microelectronics industry and computer technology, the SMD components in the electronic assembly have been widely used in the industry. Surface mount technology (SMT) is a PCB assembly technology, which means SMD components are installed directly on the surface of a printed circuit board at a specified location. No need for drilling too many holes in the PCB board. This characteristic determines the differences between the SMD and THT assembly parts, as well as the differences in the structure and performance of the process and equipment.
Now, surface mount technology is used in different fields, not only in investment electronic products but also in civil electronic products. Then why is SMT surface mount technology growing so fast? Here UETPCBA lists the following advantages of SMT.
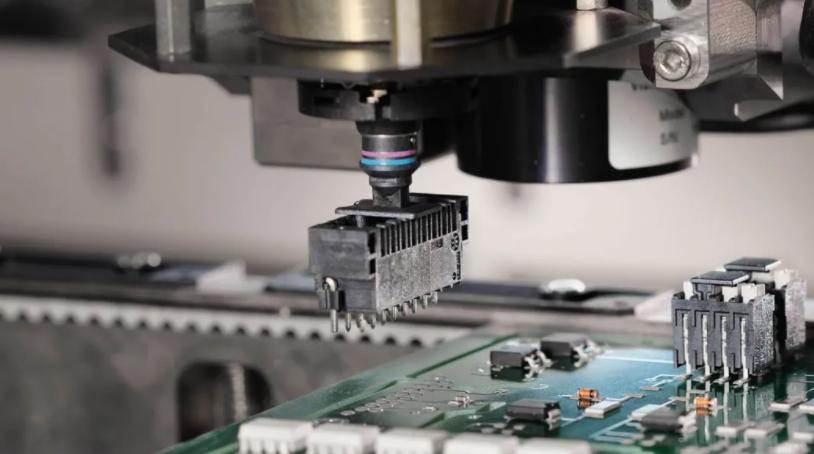
Advantages of SMT Surface Mount Technology
- High assembly density: The size and volume occupied by an SMD electronic component are much smaller than that of a through-hole component. In general, the use of SMT surface mount technology can reduce the volume of electronic products by 40% ~ 60%, and the weight is reduced by 60%~80%. When double-sided assembly on the circuit board, the assembly density can reach 5.5 ~ 20 solder joints/cm.
- High reliability: Because the soldering surface mount components of high reliability, small and light, so the seismic capability is strong, and the connection is short and the delay is small, high-speed signal transmission can be realized and used in the electronic automatic production.
- Good high-frequency characteristics: Because the SMD components are firmly mounted, and the components are usually leadless or short leads, that surface mount technology can reduce the distribution parameters of the PCB and the RF interference, also reduce the influence of parasitic for inductance and capacitance, meanwhile the high-frequency characteristics of the circuit are improved.
- Reduce the production cost
- The area used by the printed circuit board is reduced, which is 1/12 of the through-hole technology.
- Less holes drilled on the printed circuit board, saving the cost of repair.
- The cost of circuit debugging is reduced as the frequency characteristic is improved,
- Packaging, transportation, and storage costs are reduced because SMD components are small in size and light in weight.
- The SMC and SMD assembly cost are cheaper than through-hole technology.
- Full-automatic to improve production efficiency: SMD components have more standard dimensions and higher soldering consistency. The SMT surface mount technology automatic assembly technology uses vacuum nozzles to absorb and release components, improving installation density and reliability. And small components and fine pitch QFP components are also used automatic SMT surface mount technology production, to achieve automatic production, greatly improve production efficiency.
However, there are some disadvantages in SMT production.
Disadvantages of SMT Surface Mount Technology
- The nominal values on the components are not clear, which makes maintenance difficult and requires special tools or equipment to inspect it.
- Easy to cause pin deformation and soldering failure for multi-pin QFP components;
- During the operation of the electronic equipment, the thermal expansion coefficient between the component and the printed circuit board is not consistent, lead to the solder joint fails due to the expansion stress of the solder joint.
- During the reflow process, the component will be heated, and the thermal stress of the component reduces the long-term reliability of the electronic product.
- It is easier to drop or damage the parts when soldering due tothe SMD components is small.
The Basic SMT process
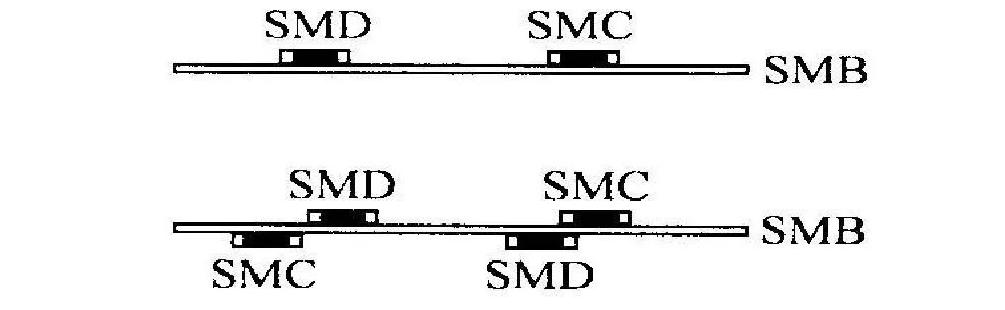
- Solder Paste Printing: It is used to leak the solder paste onto the solder pad of PCB to prepare for the soldering.
- Component Placement: It is to accurately install the surface mount components on the fixed position of the PCB.
- Solidification: Its function is to melt the adhesive, so that the surface mount components and PCB board are firmly bonded together.
- Reflow Soldering: Its function is to melt the solder paste and make the surface mount components and PCB board firmly soldered together.
- Cleaning: ts function is to remove harmful soldering residues such as flux on the assembled PCB board.
- Inspection: ts function is to test the soldering quality and assembly quality of the assembled PCB board. The equipment used is magnifying glass, microscope, on-line tester (ICT), flying needle tester, automatic optical inspection (AOI), X-ray inspection system, function tester, etc.
Single-side PCB assembly
Incoming Material Inspection => Solder Paste Printing => Component Placement => Baking(solidification)=> Reflow Soldering =>Cleaning => Inspection => Repair
Single-side mixing assembly
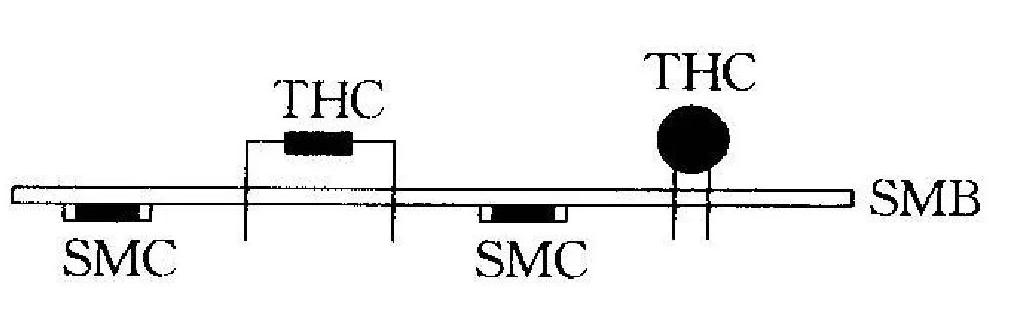
Incoming Material Inspection => Solder Paste Printing => Component Placement => Baking(solidification)=> Reflow Soldering => Cleaning => DIP Insert => Wave Soldering => Cleaning => Inspection => Repair
Double-side PCB assembly
Incoming Material Inspection => Solder Paste Printing(A side)=> Component Placement => Baking(solidification)=> Reflow Soldering (A side) => Cleaning => Solder Paste Printing(B side)=> Component Placement => Baking(solidification)=> Reflow Soldering (B side) => Cleaning => Inspection => Repair
Double-side mixing assembly
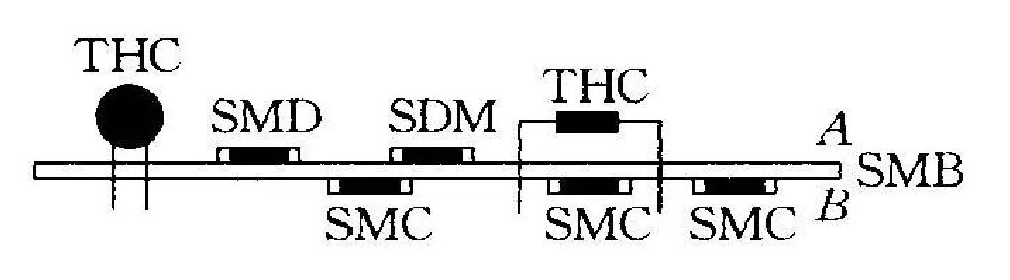
A: Incoming Material Inspection => Solder Paste Printing(B side) => Component Placement => Baking(solidification)=> DIP Insert (A side)=> Wave Soldering => Cleaning => Inspection => Repair. SMD parts first and then DIP insert, suitable for SMD components more than DIP components
B:Incoming Material Inspection => DIP Insert (A side) => Solder Paste Printing(B side) => Component Placement => Baking(solidification) => Wave Soldering(A side) => Cleaning => Inspection => Repair. DIP parts first and then SMD parts, suitable for DIP components more than SMD components.
C:Incoming Material Inspection => Solder Paste Printing(A side) => Component Placement => Baking(solidification) => Reflow Soldering => DIP Insert => Solder Paste Printing(B side) => Component Placement => Baking(solidification) => Wave Soldering(A side) => Cleaning => Inspection => Repair. suitable for A side mixing technology,B side surface mount technology.
D:Incoming Material Inspection => Solder Paste Printing(B side) => Component Placement => Baking(solidification) => Solder Paste Printing(A side) => Component Placement => A Reflow Soldering(A side) => DIP Insert => Wave Soldering(B side) => Cleaning => Inspection => Repair. suitable for A side mixing technology,B side surface mount technology, first to double side SMD parts,then reflow soldering,DIP soldering,and wave soldering.
E:Incoming Material Inspection => Solder Paste Printing(B side)=> Component Placement => Baking(solidification) => Solder Paste Printing => Solder Paste Printing(A side) => Component Placement => Baking(solidification) =>Reflow Soldering ( A side)=> DIP Insert(B side) => Wave Soldering(B side)(If there are few DIP components, manual soldering can be used)=> Cleaning => Inspection => Repair. suitable for A side surface mount technology 、B side mixing technology.
SMT Assembly Service in UETPCBA
We offer all the advantages of turnkey PCB manufacturing and full turnkey PCB assembly (SMT assembly and THT assembly) service with fast turnaround times and an affordable budget.
Our primary mission is to continually provide high-quality PCB &PCB Assembly services that make us the best choice for your electronic manufacturing. If you have any SMT PCB assembly projects or turnkey PCB assembly projects please feel free to contact us at: [email protected].