With the rapid development of various electronic industries, including the field of components, the functions of electronic products have gradually improved. Global competition has led manufacturers of these products to shorten their product market response time to respond to the ever-increasing expectations and requirements of customers for new products. This trend poses certain challenges to the traditional welding technology of various electronic components. In order to meet market demand, in welding technology, it can be said that the technology is improving, and the welding methods are also more diversified. Our common ones are wave soldering, laser soldering and selective soldering. By comparing traditional wave soldering methods, selective soldering and laser soldering methods, we have a clearer understanding of the convenience brought to us by technological innovation.
Introduction to Selective Soldering:
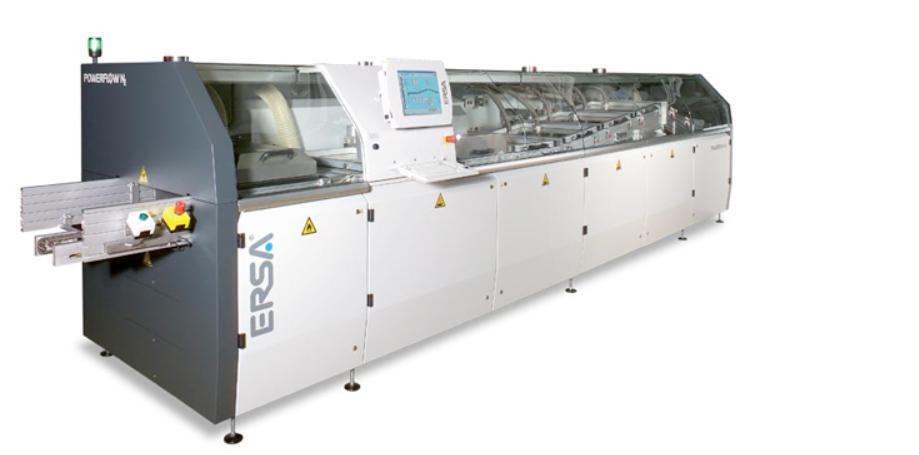
Unlike traditional wave soldering where the lower part of the PCB is completely immersed in liquid solder, selective wave soldering machine only has a specific area in contact with the solder. In the selective soldering process, the position of the solder head is fixed, and the manipulator drives the PCB to move in all directions.
Selective soldering is the production line type of industrial batch production mode, soldering nozzles of different sizes can be used in batch soldering, usually soldering efficiency can be improved more than dozens of times than manual soldering (depending on the specific circuit board design).
Selective soldering machine applies equipment in the field of PCB plug-in through-hole soldering. Due to different soldering advantages, in the PCB through-hole soldering field in recent years, it has gradually become a popular trend of through-hole soldering.
Selective Soldering Features:
- Nitrogen closed-loop control
- FTP network connection
- Optional double position nozzles
- Design of three modules of flux, preheating and soldering
- Flux spraying, wave peak height with calibration tool
- Gerber file import, can be programmed offline
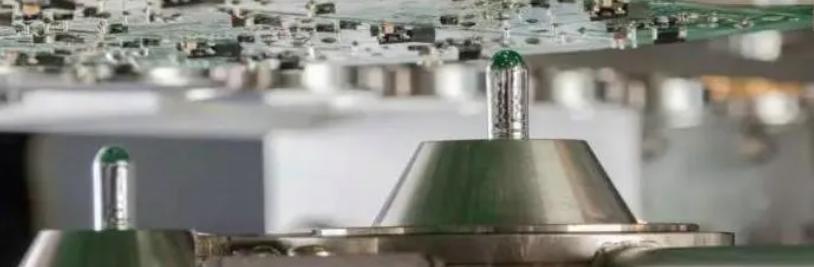
Advantages of Selective Soldering:
- High production efficiency and high automation in the soldering of through-hole components
- Selective soldering can accurately control the location and quantity of flux spraying
- Accurate control of microwave peak height
- Precise control of soldering position without shielding certain components
- Nitrogen protection of microwave peak surface
- According to the optimization of process parameters of each solder joint, the nozzles of different sizes can be replaced quickly
- Single solder joint or component can be performed by setting different parameters for each component as required
- A variety of preheating modules (infrared, hot air) and an additional preheating module above the board are available
- Selective Soldering machine eliminates the need for expensive aperture wave soldering trays
- The selection of structural materials is perfectly suitable for the application of lead-free solder
- Selective soldering’s modular design reduces maintenance time
- Precise set flux spray, applied only to pads and pins, can ensure high cleanliness of PCB board, no need for additional cleaning
Disadvantages of Selective Soldering:
1.Selective soldering has a limited range of applications, only suitable for PCB assembly process of through-hole design, but not for SMT and CABLE WIRES.
2.Due to the need to use flux and generate tin slag during soldering, the later production cost is high.
3.The function of selective wave soldering is more complex than that of normal wave soldering,so the cost of purchasing equipment and manufacturing is higher.
Introduction to Wave Soldering:
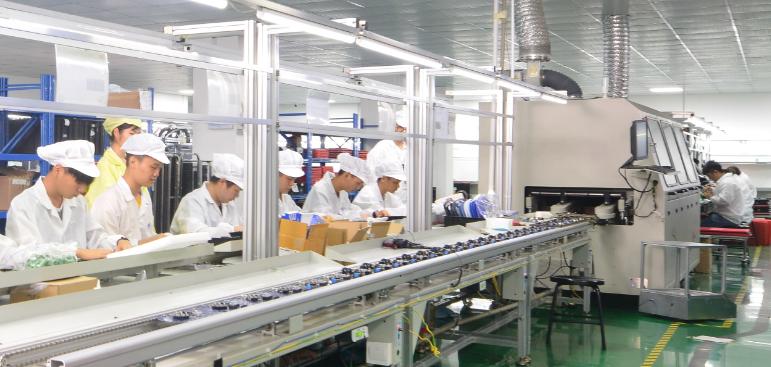
Wave soldering machine is suitable for soldering large area and large quantity printed circuit boards and has been widely used in the industrial production of electronic product soldering. Wave soldering is to make the soldering surface of the plug-in PCB directly in contact with the high-temperature liquid tin to achieve the purpose of soldering, the high-temperature liquid tin to keep the inclined plane, and by the special device to form a similar phenomenon of the liquid tin wave, so it is called “wave soldering”.
The main material of wave soldering is tin bar. The wave soldering process must have a specific angle and a certain immersion depth. Wave soldering is the process of melting the liquid solder, forming a solder wave of a specific shape on the surface of the solder tank with the help of a pump, inserting the PCB of the component into the transmission chain, and soldering the spot by soldering the wave. The wave soldering machine is mainly composed of a transport belt, flux spray area, preheating area, and wave tin oven.
Advantages of Wave Soldering:
- Improve production efficiency and reduce costs.
- Improve the solder joint quality and reliability
- Improve the operating environment and the health of the operator
- Product quality standardization
- Can complete the work which manual operation can not complete.
- Wave soldering has it’s advantageous for mass production
Disadvantages of Wave Soldering:
- Consume a lot of flux and solder
- Wave soldering requires a lot of power
- wave soldering needs to be reworked after wave soldering
- High operating cost
- Need to clean equipment regularly leads to complex equipment maintenance and maintenance work.
- The poor design of printed circuit board makes production difficult
Introduction to Laser Soldering:
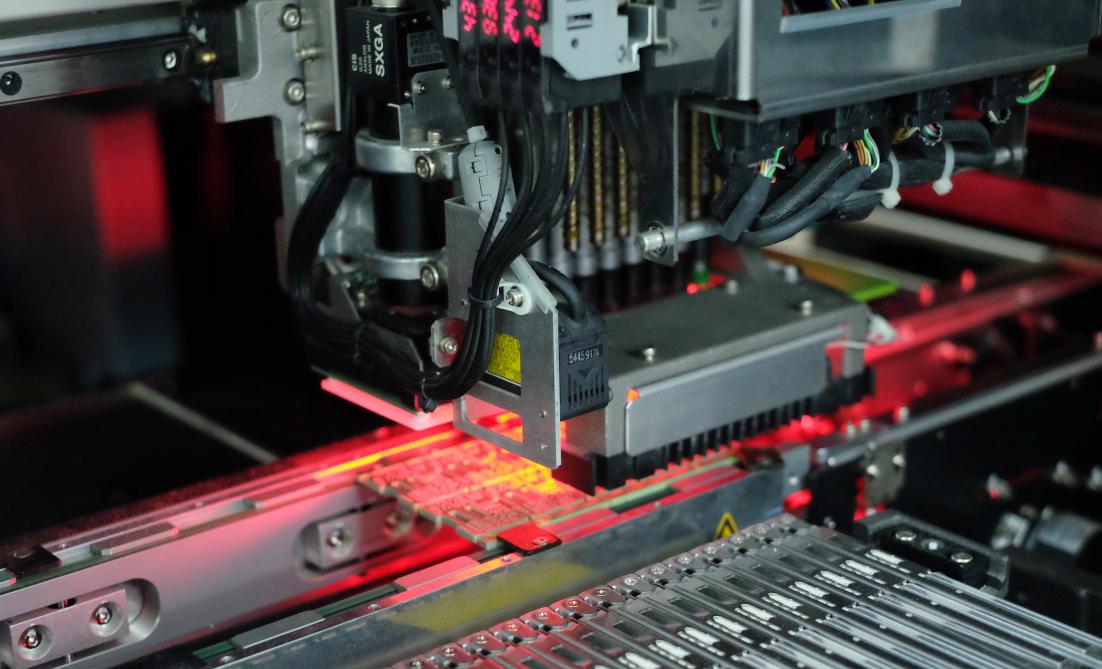
The light source for laser soldering machine uses laser light-emitting diodes, which can be focused precisely on the solder joint through an optical system. The advantage of laser soldering machine is that the energy required for soldering can be precisely controlled and optimized. It is suitable for selective reflow soldering process or the use of tin wire connector. For SMD components, solder paste should be applied first and then soldered.
The laser soldering process is a two-step process: first the solder paste is heated and the solder joints are preheated. The solder paste used for soldering is then completely melted, and the solder is completely wetted to the pad, resulting in a soldering. The use of laser generator and optical focusing assembly soldering, energy density, high heat transfer efficiency, non-contact soldering, especially suitable for soldering small solder joint or small solder joint power, energy saving.
Laser Soldering Features:
- Positioning accuracy
- Small laser spot, pad, spacing small component soldering advantages
- Non-contact soldering, no mechanical stress, electrostatic risk
- No tin slag and flux waste, low production cost
- Various types of solderable products (SMD, PTH, cable wires)
- More solder options (solder paste, tin wire, tin ball)
Advantages of Laser Soldering:
- Laser soldering can be used in ultrafine electronic PCB and multilayer components, traditional solderingtechnology has been unable to apply.
- Laser soldering can complete the soldering for ultra-small parts, traditional soldering iron cannot realize.
- “Non-contact soldering” is the biggest advantage of laser soldering, which will not cause a physical burden.
- Effective heating with a laser beam is also an advantage, which can be used to irradiate narrow parts that cannot be accessed by the soldering iron and to change angles when there is no distance between adjacent components in a dense assembly.
- Laser soldering requires very few replacement parts and low maintenance cost.
Tips from professional PCBA manufacturer: UETPCBA
For printed circuit boards with through-hole components and large surface-mount components, wave soldering is a good option, but a selective soldering process is available for densely populated boards. Therefore, when we choose PCBA partners, we need to customize the corresponding soldering process according to the requirements. Whether it is wave soldering or selective wave soldering processing, only the experienced PCB assembly factory can be selected to maximize the guarantee of PCB board soldering quality.
UETPCBA provides professional PCB assembly services, relying on rich soldering experience, coupled with advanced equipment and technical capabilities, so that our services not only have quality advantages, but also time-guaranteed, can meet customers’ needs of rapid delivery from prototyping to mass production.