Printed circuit board is one of the largest and most important devices in electronic products, its performance sometimes directly determines the success or failure of the product. Each PCB is different, so many of their features and PCB board prices are also different. Therefore, the China pcb manufacturer price is also different. So what are the various factors that affect the pcb board price and pcb assembly cost? How much does a circuit board cost?
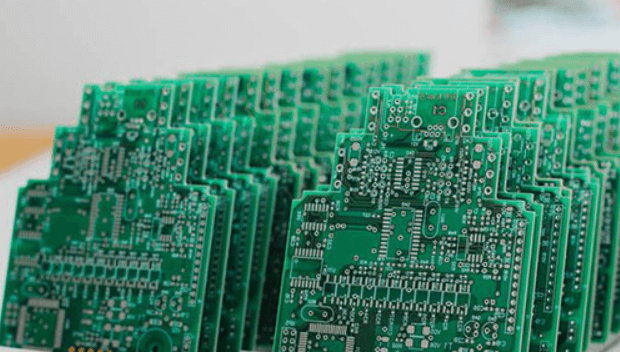
Influencing factors of circuit board cost
1, PCB material
The common PCB board material is generally FR4, Aluminum, Rogers, FPC/Rigid-Flex, the thickness of the board from 0.2mm to 4.8mm; In addition, the solder mask using the most common solder mask or the photosensitive green solder mask also has a certain impact on the price. The PCB material is different, the pcb board cost is also different. Some substrate and laminate PCB materials different, if high performance needed, then your materials cost will be more expensive than others. All these in a PCB board, it may cause a big difference on the pcb board price and pcb assembly cost.
2, The Dimension of the PCB
Different sizes of PCB board lead to different pcb board prices, that is to say, the larger material needed to make a PCB, the more expensive it will be. On the contrary, it will low cost pcb assembly.
3, The number of PCB layers
The number of PCB layers directly affects the pcb board price. The more layers, the more expensive. Most the high-speed PCB are generally multilayer layers. PCB layers are different, PCB cost and PCB assembly cost will also be different.
4, Surface treatment
The differences between the surface treatment process will also affect the pcb board price and pcb assembly price.
Common surface finish: HASL with lead, HASL lead free, Immersion gold (ENIG), OSP, Hard gold, Immersion silver (Ag), ENEPIG, and some combination process, etc., the above differences in each process have great influence on the price, such as ENIG process is more expensive than HASL with lead.
5, Via(hole) Process and quantity
Different structure of vias has different pcb board price. Such as, the price of through hole vias will be lower than back drilling, the back drilling price is lower than the blind/ buried vias, the price of the small size hole is higher than the large one, and so on.The more vias on the PCB board, the more expensive it will be. On the contrary, there will be low cost pcb assembly,
6, PCB Complexity
PCB Complexity means fabrication difficulty, a PCB with 0.3mm holes and less than 0.2mm holes, then the two specifications of the hole will form different drilling costs.If the holes are smaller than 0.15mm, like 0.1mm, then laser drilling is needed, which is more expensive than mechanical drilling.And the min track/spacing also influence the price, for example, normally many PCB manufacturers standard track width is 4mil, and the customer requires it to be 2.5mil. In this case, the price will certainly be much higher.Moreover, some circuit board is not a conventional process, such as half hole, buried blind hole, Via in pad/ Via filled with resin, carbon mask, impedance control and edge Plating and so on, this kind of design also increase the cost.
7, Copper thickness
Common copper thickness: 1/2oz, 1OZ, 2OZ, 3OZ, 4OZ, etc., the higher thickness of the copper, the more expensive the board will be.
8, Quality standards
The commonly used quality acceptance standards for customers are: IPC2, IPC3, military standard and so on. The higher standards, the more expensive the board will be.
9, Speed
If you require printed circuit board rapid prototyping and manufacturing to meet your deadlines, some PCB factories can provide expedited service for fabrication (like our UETPCB, we can provide expedited 12H,24H,48H manufacturing service), then the pcb asembly cost will be different.
10, Quantity
The more quantity of PCB, the cheaper it will be. That’s why, the unit price of PCB prototype cost is always higher than the mass production, because more quantity will share the engineering cost, labor cost and so on.
11, Testing method and cost
PCB board is required to use the flying probe test in PCB prototype process.When mass production the test frame is needed to test, it’s faster but more expensive.And the cost is different if you choose the full inspection or sampling inspection.
How is PCB assembly cost calculated?
How much does a circuit board cost?
PCB assembly cost =PCB board cost + component procurement cost +SMT/DIP soldering cost +PCBA test cost + special packaging and logistics cost.
Next, we will talk about some factors that affect PCB assembly cost and how to reduce the PCB assembly price
1, PCB cost
All factors we have mentioned above.
2, Component procurement cost
Component procurement cost is a part of pcb board cost. Components Procurement cost is the mainly cost in PCBA SMT Processing. The PCBA manufacturer purchases the components according to the BOM.
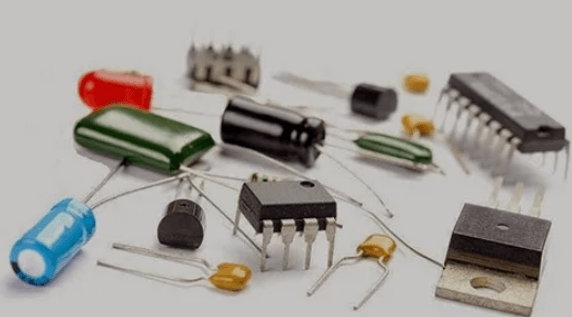
3, Number of solder pads
Solder pads cost is a part of pcb board cost. The number of solder pads is the decisive factor in SMT price. Now the SMT quotation is basically in accordance with the number of solder pads to calculate, the more solder pads, the price is higher. The solder pads are different, the pcb assembly cost is also different.
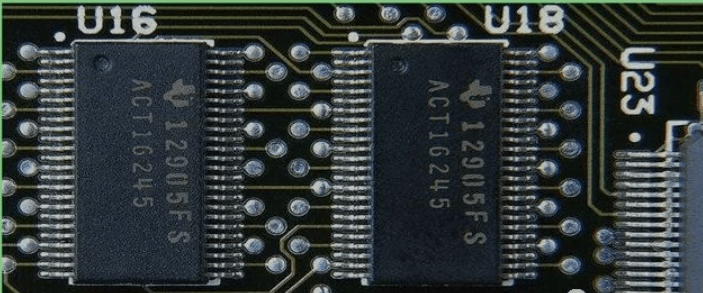
4, Engineering cost/set-up cost
Engineering cost is a part of pcb board cost. A few years ago, there were engineering cost/set-up costs, especially in the small quantity orders, factories often charged that, now these costs are included in the PCB assembly cost and SMT cost.
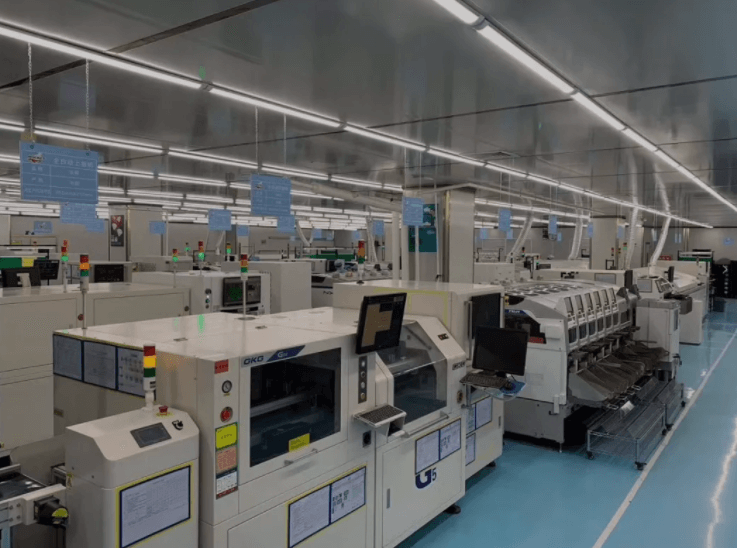
5, Stencil cost
Stencil cost is a part of pcb assembly cost.Stencil is needed in the PCB assembly process, you can choose the frameless stencil or framed stencil. Framed stencil is a little more expensive than frameless one. In the PCBA factory we used framed stencil, you can use the frameless stencil for your prototyping or DIY soldering at home to reduce the cost.
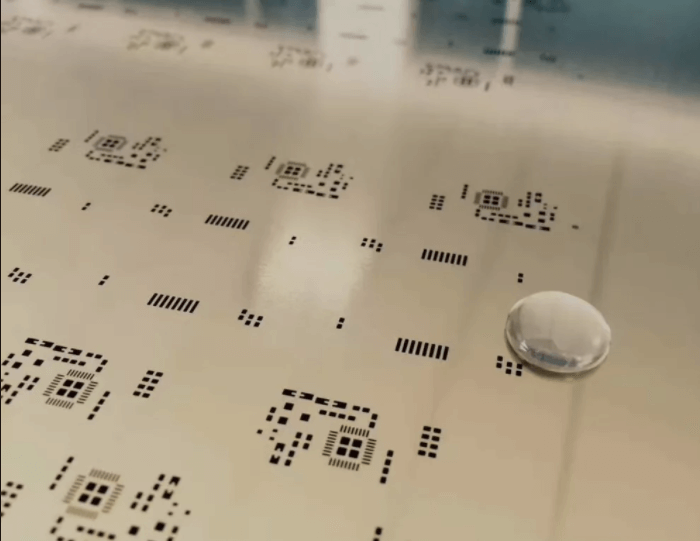
6, Expedited turnaround time cost
Expedited turnaround time cost is a part of pcb board cost. In the PCBA factory, the order will be arranged according to placing time. If customers need expedited finish the assembly with a short time, then they will be charged expedited cost.
7, SMT assembly cost (SMD+DIP)
SMT assembly cost is a part of pcb board cost. Another key aspect of PCBA pricing is the type of assembly technology used.Surface mount technology (SMT) can save money due to low installation costs and high precision of automation.The DIP soldering will cost more as this process need more manual soldering, so labor cost will be added, and pcb assembly price will be high.
8, PCBA testing cost
PCBA testing cost is a part of pcb fabrication cost. If customers need extra PCBA function test or programming, the extra PCB testing fee will be charged.
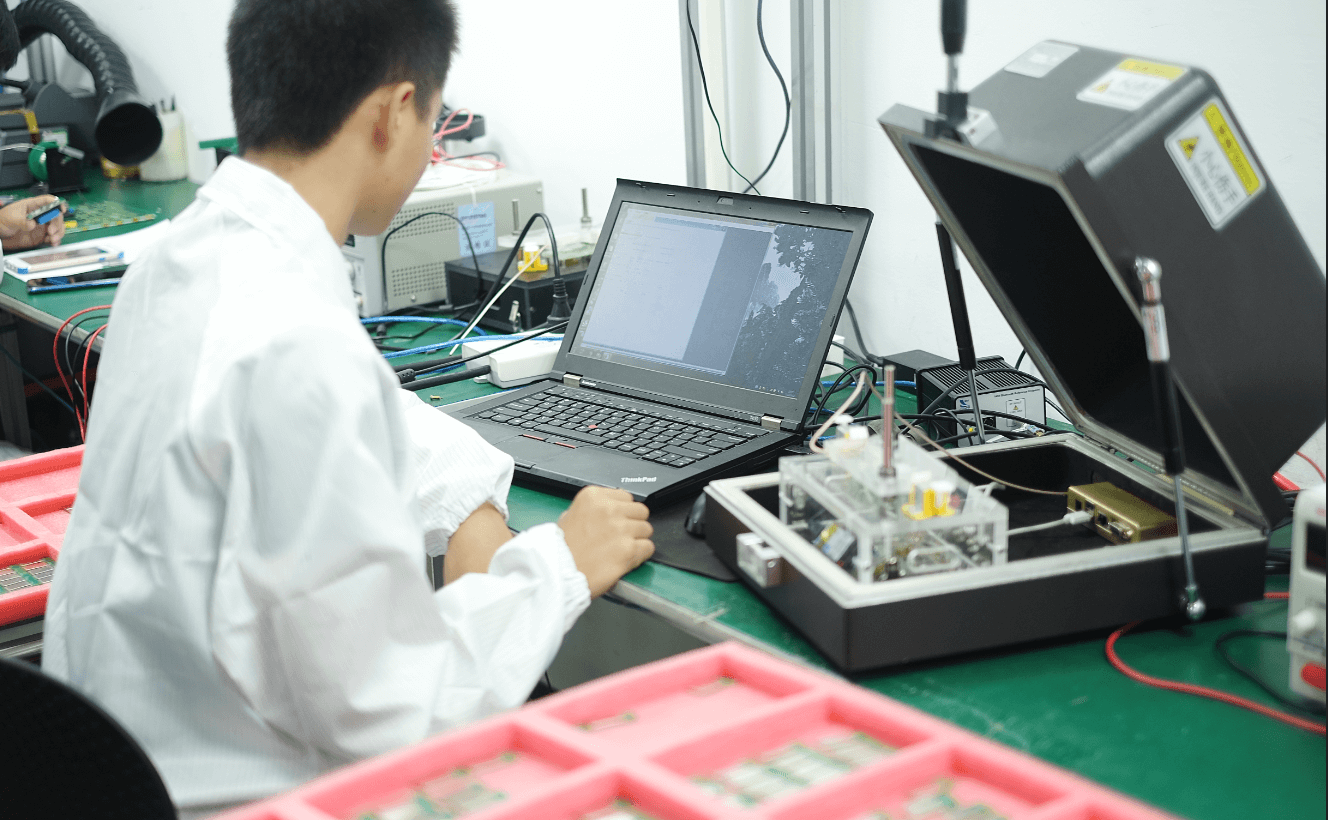
9, Quantity
Quantity is a part of pcb assembly cost. On the manufacturing side, large quantities lead to lower assembly costs due to economies of scale. In other words, when the product is mass-produced, the unit price per PCB will be greatly reduced. In the long run, increasing the number of printed circuit boards can save cost for companies by avoiding unnecessary one-time costs.
10, Labor cost
Labor cost is a part of pcb assembly cost. In each process of PCB assembly, there need manual work, especially in the DIP soldering process, so labor cost takes mainly part.
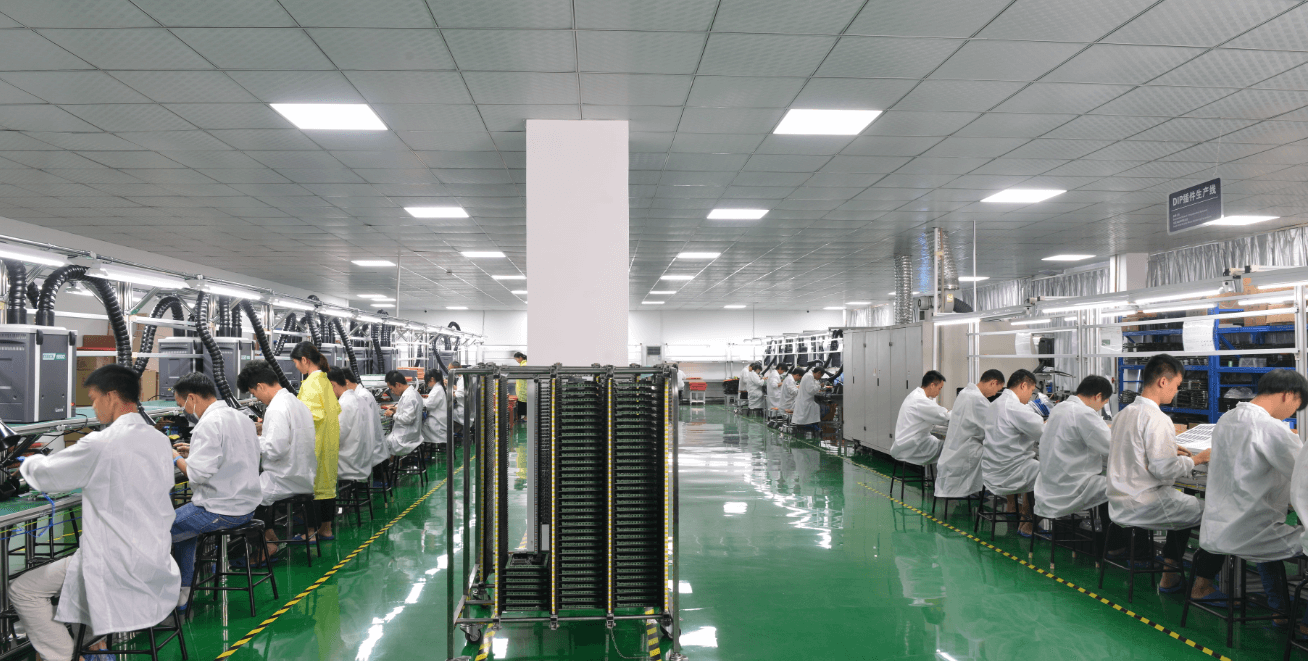
How to save the PCB assembly cost?
1,Standard size of PCB board
The smaller the size, the lower the pcb board price. Part of the PCB size has formed a minimum standard, and the standard size of PCB board can effectively reduce the cost.
2, Using SMT parts
Using SMT parts, then more components can be placed on the PCB board, and using SMT assembly will be less costly than using plug-in parts (DIP).
3, The number of layers of PCBA board:
The more layers, the higher the cost, the PCB with fewer layers will usually increase the size requirements, so under the premise of ensuring that the size of PCBA meets the requests, the appropriate fewer layers of PCB board can effectively reduce the cost.
4, Drilling
The more holes in the design, the more time needed during the PCB fabrication, so the less holes on the PCB, the more time and money you can save.
5, Blind hole
Generally, the blind hole is more expensive than the through hole, which requires higher technical cost. Therefore, when the through hole is available instead, the through hole can be selected to effectively reduce the cost.
Conclusion
There are many pcb manufacturers in China, and the china pcb manufacturer price will be different because of the degree of professionalism of each manufacturer.
As one of the most professional PCB assembly companies in China, we have focused on PCB design, PCB production, component procurement, SMT assembly, PCBA testing, conformal coating, Box Build assembly and other one-stop electronics manufacturing services for more than 15 years. Moreover, in terms of price, UETPCBA provides low cost pcb assembly. We will not depress quality because of low cost pcb assembly. On the contrary, our quality can be trusted.