In the process of PCBA production, it depends on many machinery equipment to finish a board assembly. Therefore, the quality level of equipment in a factory directly determines the manufacturing ability. Here are mainly introduces the basic equipment of universal PCBA factory.
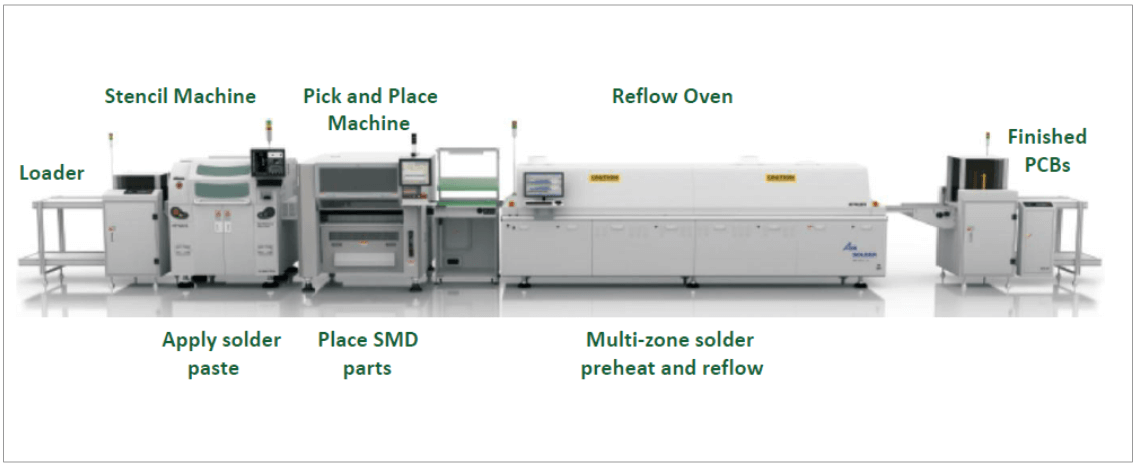
The basic equipment required for PCBA production is the solder paste printer, SMD machine, reflow soldering machine, AOI inspection, component lead cutting machine, Wave soldering, X-Ray test, ICT test fixture, FCT test fixture, HALT test fixture, etc. Different PCBA factories equipped with machinery equipment will be different.
The main PCBA production equipment in following.
PCB Washing machine
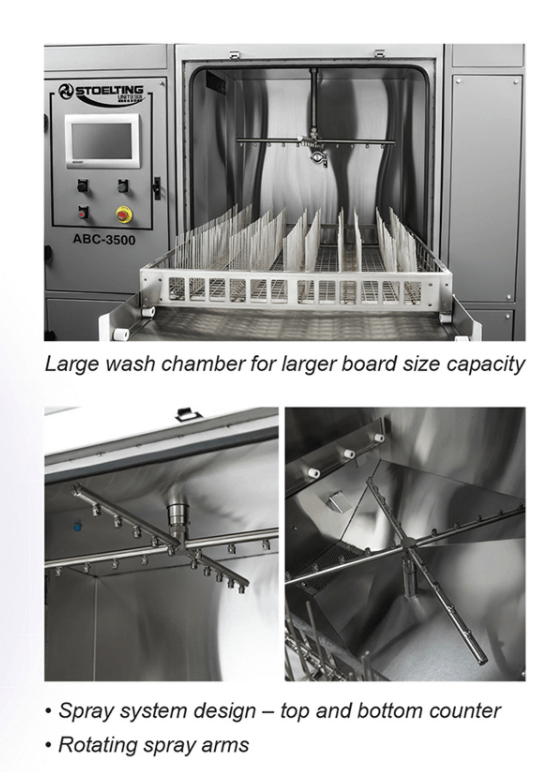
PCB board is not strictly cleaned when leaving the PCB production workshop, there is a lot of dust remain on PCB board surface, edge, through hole and other places.
PCB board is easy to generate static electricity in the process of manufacturing, which makes it easy to cause static electricity injury or dust adsorption in the (PCB assembly) SMT process.
Dust and other foreign matter can cause paste printing defects and soldering defects such as cold soldering, empty soldering, component warping, deviation and so on.
The PCB bare boards entering the washing machine before SMT process can prevent and reduce the generation of defective products, improve the quality, and achieve the purpose of enhancing product reliability.
Automatic Solder Paste Printer
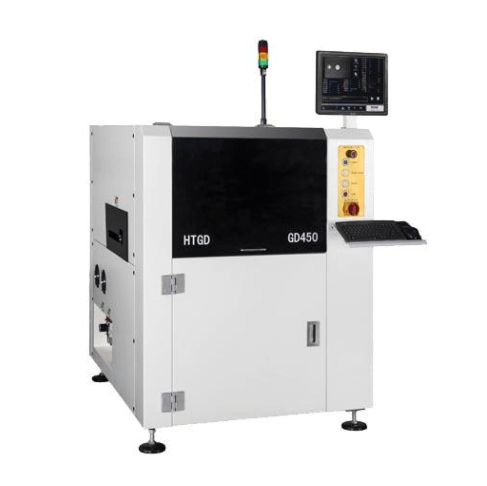
Modern solder paste printer generally consists of loading, solder paste adding, solder paste printing, input SPI Inspection and other mechanisms.
It’s working principle is as follows: firstly, the PCB board is fixed on the printing positioning platform, and then the left and right scraper of the printing machine will leak the solder paste or red glue through the stencil to the corresponding solder pad, and then the PCB board which printed the solder paste will be transferred to SPI Inspection for detection.
SPI (Solder paste inspection)
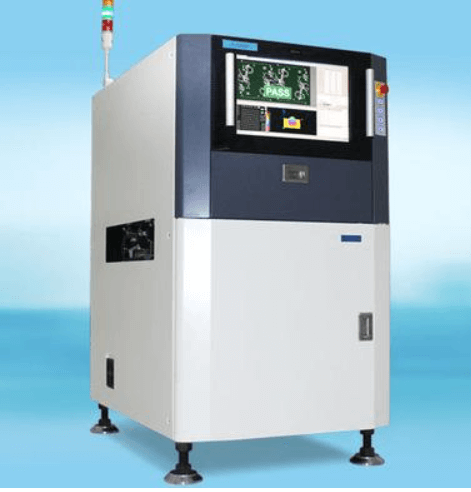
SPI is for the solder paste printing quality inspection and printing process verification and control.
Its basic functions are as follows:
- Find out the quality defects of solder paste printing in time. SPI can directly tell the user which solder paste printing is good or bad, and provide a hint of the types of defects.
- Through a series of solder joint inspection, the quality trend is found to change. SPI detects quality trends through a series of solder paste inspection, and identifies the underlying factors that cause such trends before the quality is out of range, such as adjustable control parameters, human factors, solder paste variation factors, etc. Then timely adjustment, control the trend to continue to spread.
Finally, the detected PCB board with good solder paste printing are transported to the Pick& Placement machine.
Pick& Placement machine
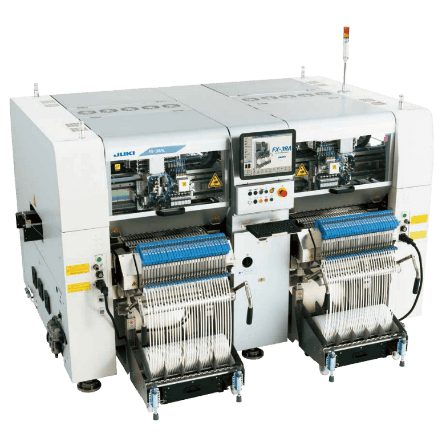
Pick & Placement process also called Surface Mount System. In the PCB assembly process line, it is placed behind the solder paste printer and is an equipment for placing the SMD type components accurately on the PCB pad by moving the mounting head.
Divided into two types: manual and automatic ,automatic one including normal machine, low, medium, high speed SMD machine. Finally, the assembled PCB boards with the installed components will be transported to reflow soldering through the visual inspection transmission platform.
Reflow Soldering
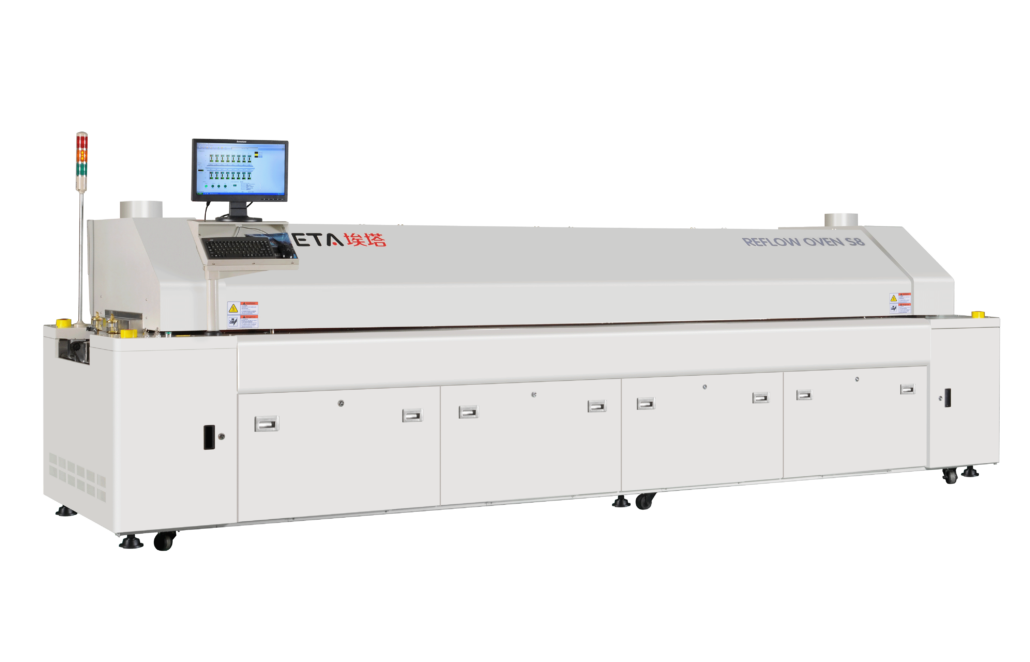
There is a heating circuit inside the reflow soldering, it can heat air or nitrogen to a high enough temperature and then blow to the PCB board that has been soldered with the components, so that the solder paste on both sides of the component will be melted and solidify to the PCB board.
The advantages of this process are that the temperature is easily controlled, oxidation is avoided during soldering, and manufacturing costs are more easily controlled.
Automated Optical Inspection (AOI)
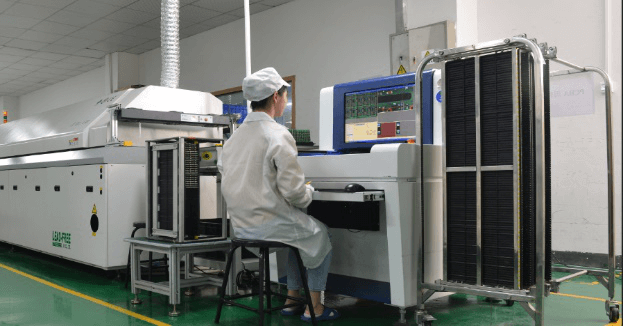
Automatic Optic Inspection is based on optical principle to detect common defects encountered in PCB assembly production equipment. AOI is a new emerging testing technology, but developed rapidly, many PCB manufacturers have launched AOI testing equipment. When automatic detection, the machine will scan the PCB automatically through the camera, collect images, compare the tested solder joints with the qualified parameters in the database, check the defects on the PCB after image processing, and display/mark the defects through the display or automatic signs for maintenance personnel to repair.
Component lead cutting machine
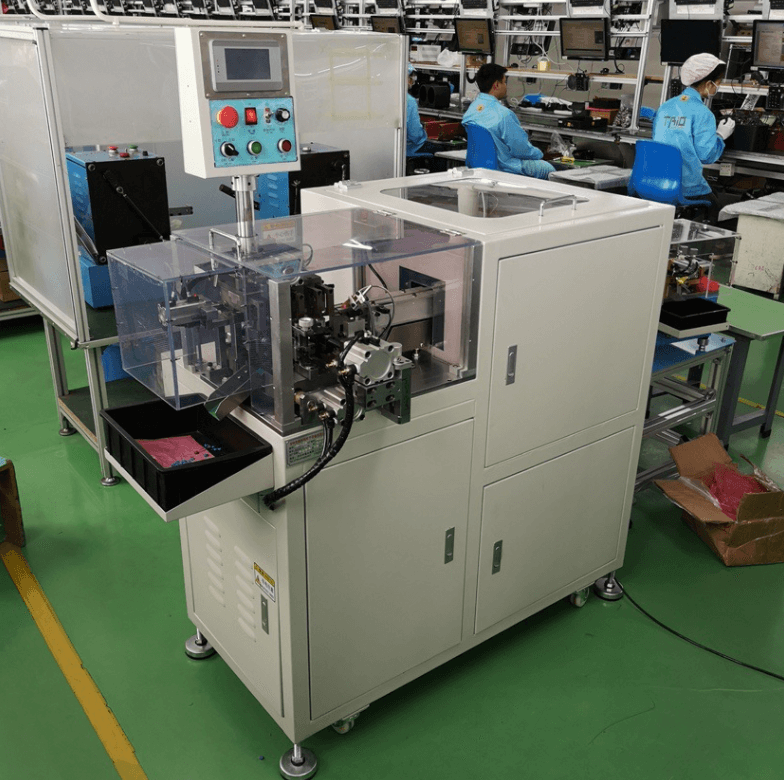
It is used for cutting and deforming for the soldering pins of DIP components.
Component insertion machine
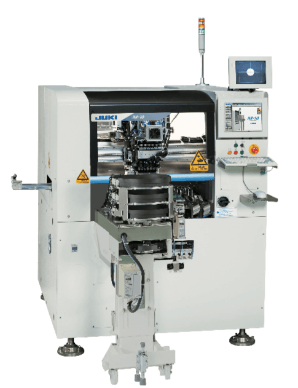
It is a mechanical device that automatically inserts some regular DIP components (also called “automatic insert machine”) into the through hole of PCB board.
Wave soldering
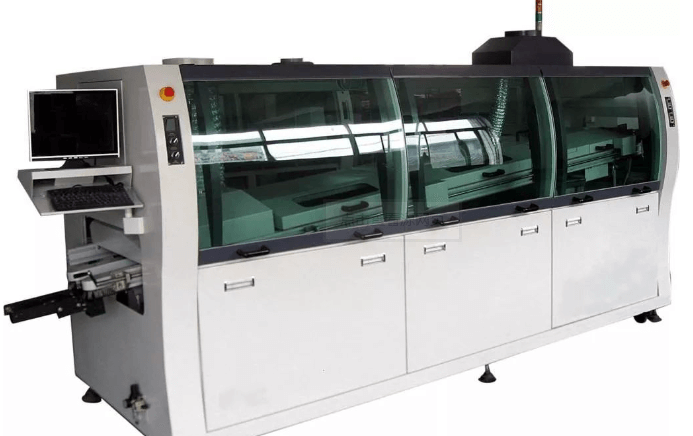
Wave soldering is to make the soldering surface of the plug-in through holes directly contact with the high temperature liquid tin to achieve the purpose of soldering.
The high temperature liquid tin to maintain a bevel, and by a special device to form a similar wave of liquid tin phenomenon, so it is called “wave soldering”, the main material is the solder bar.
Post-Wave soldering Automated Optical Inspection (AOI)
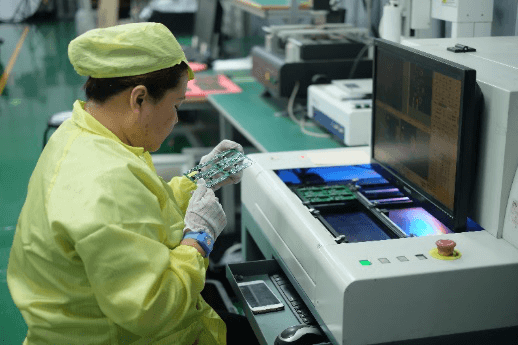
Because of the characteristic of the wave soldering process, in this process is the most likely to produce defects, such as soldering pins shorting, faulty soldering, missing soldering, etc., and with the PCB assembly process is more and more miniaturization, high precision, the original manual visual inspection has been completely restricted the production capacity and quality of development, professional machine view is used to replace artificial has higher stability and reliability.
X-Ray BGA Inspection
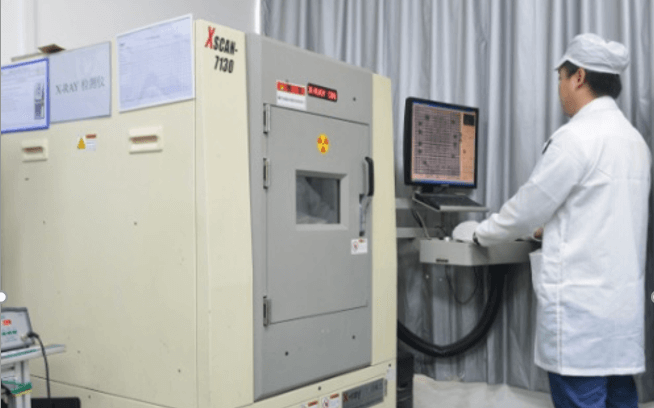
This testing is commonly performed on Quad-flat No-lead (QFN) PCBs, and Ball Grid Arrays (BGAs) in PCBA process.
X -ray inspection has advantages of fast speed, high efficiency, low cost, no damage to the sample.
First Article Inspection
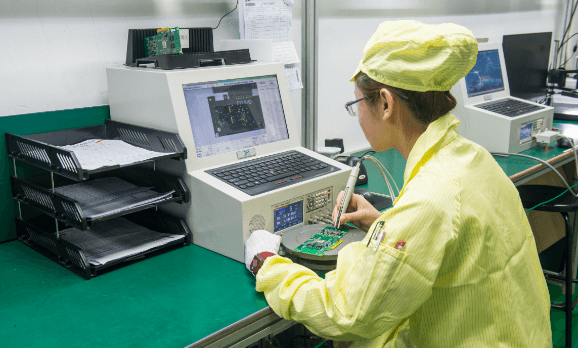
Import the BOM, coordinate, designator or scan picture into the application software to generate a test program. Cooperate with the sophisticated LCR measuring instrument to measure each component according to the BOM.
The software automatically sets the LCR tap position, automatically compares the actual value of the component, automatically marks the automatic voice prompt PASS, and automatically generates the first article inspection report.
PCBA Washing machine
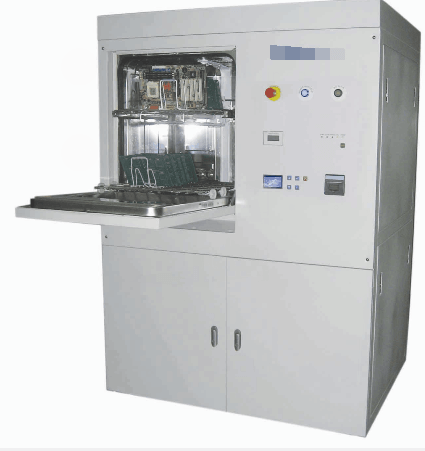
PCBA Washing machine used for cleaning PCB assembled (PCBA) board, can remove the residue after soldering.
Sensitive Component Storage Cabinet
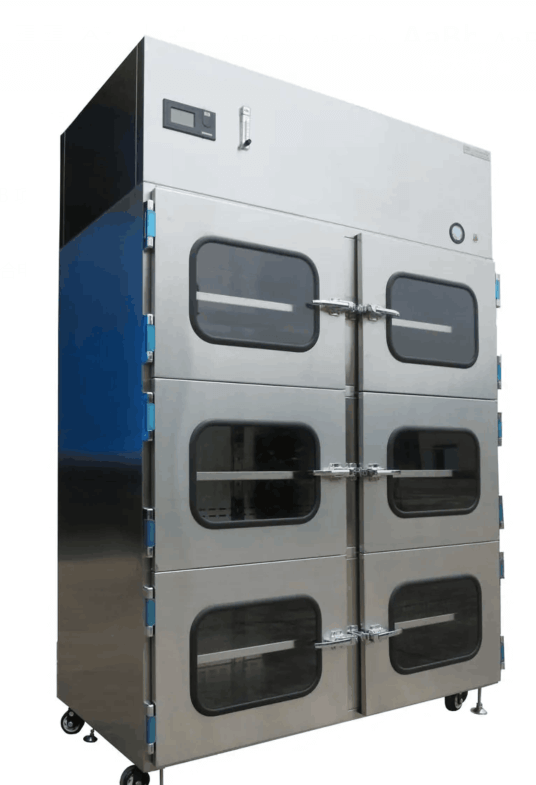
The sensitive component storage cabinet is used for keeping the sensitive components.
Such as thermosensitive, photosensitive, electric pressure sensitive, pressure sensitive, magnetic sensitive, gas sensitive, humidity sensitive components.
FCT test fixture
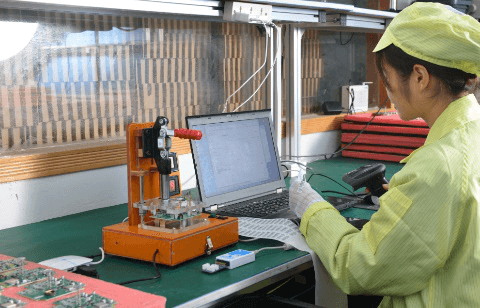
FCT test fixtures mainly perform functional tests on PCBA products, such as voltage, current, power and frequency.
FCT test fixtures can test semi-finished products or finished products. Nowadays, FCT test fixture control mode is mainly automatic, and this kind of control mode has a very fast fixture test speed and accurate test data.